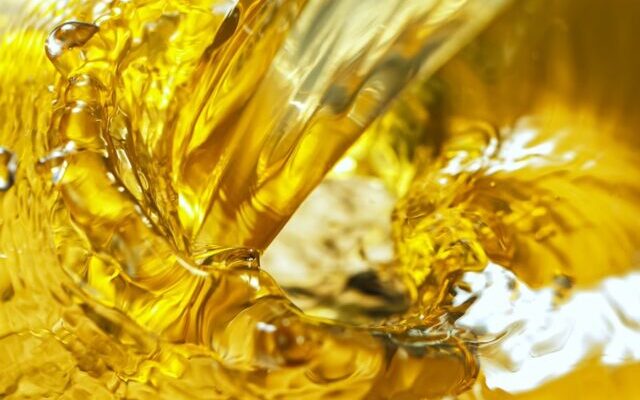
Introduction
Adhesives have become an integral part of our daily lives, quietly holding together the world around us. From the furniture in our homes to the cars we drive, adhesives play a crucial role in ensuring everything stays in place. Among the various types of adhesives available, rubber-based adhesives stand out for their versatility and effectiveness. At Super Bond Adhesives, we pride ourselves on providing top-notch rubber-based adhesive solutions tailored to meet diverse needs. In this comprehensive guide, we will explore the fascinating world of rubber-based adhesives, delving into their composition, applications, benefits, and how they compare to other adhesive types.
What Are Rubber-Based Adhesives?
Rubber-based adhesives are a class of adhesives formulated using natural or synthetic rubber as the primary bonding agent. These adhesives are known for their excellent flexibility, durability, and ability to bond to a wide range of surfaces. The rubber component imparts unique properties to the adhesive, making it suitable for various industrial, commercial, and household applications.
Composition of Rubber-Based Adhesives
The primary ingredient in rubber-based adhesives is either natural rubber or synthetic rubber. Natural rubber is derived from the latex of rubber trees, while synthetic rubber is produced through the polymerization of specific monomers. These rubbers are mixed with various additives, including tackifiers, plasticizers, fillers, and solvents, to enhance their performance characteristics.
- Tackifiers: These are resins that increase the adhesive’s stickiness or tack, allowing it to adhere quickly to surfaces.
- Plasticizers: These additives improve the flexibility and workability of the adhesive, ensuring it remains pliable over time.
- Fillers: Fillers such as calcium carbonate or silica are added to modify the adhesive’s viscosity and provide additional strength.
- Solvents: Solvents help dissolve the rubber and other components, creating a uniform mixture that can be easily applied.
Types of Rubber-Based Adhesives
Rubber-based adhesives come in various forms, each tailored for specific applications and requirements. The two main categories are:
1. Pressure-Sensitive Adhesives (PSAs)
Pressure-sensitive adhesives are designed to bond instantly to surfaces with light pressure. They do not require heat, water, or solvents to activate the adhesive properties. PSAs are commonly used in tapes, labels, and stickers. At Super Bond Adhesives, our PSAs are engineered to provide strong, durable bonds while remaining easy to handle and apply.
2. Contact Adhesives
Contact adhesives, also known as contact cements, require application to both surfaces to be bonded. Once applied, the surfaces are allowed to dry until they become tacky. The adhesive bond is formed when the surfaces are pressed together. Contact adhesives are ideal for bonding large surface areas and materials such as laminates, veneers, and rubber.
Applications of Rubber-Based Adhesives
The versatility of rubber-based adhesives makes them suitable for a wide range of applications across various industries. Here are some key areas where these adhesives excel:
1. Automotive Industry
Rubber-based adhesives are extensively used in the automotive industry for bonding interior and exterior components. They provide strong, flexible bonds that can withstand vibrations, temperature fluctuations, and exposure to chemicals. Common applications include attaching weatherstripping, trim, upholstery, and gaskets.
2. Construction and Building
In the construction industry, rubber-based adhesives are valued for their ability to bond diverse materials such as wood, metal, glass, and plastics. They are used in flooring installations, sealing joints, and assembling prefabricated components. The adhesives’ flexibility ensures that they can accommodate the natural movements of building materials without compromising the bond.
3. Packaging and Labeling
Rubber-based pressure-sensitive adhesives are widely used in the packaging and labeling industry. They provide quick and reliable bonding for labels, tapes, and packaging materials. The adhesive’s ability to adhere to various surfaces, including cardboard, plastic, and metal, makes it a preferred choice for packaging applications.
4. Footwear and Leather Goods
The footwear and leather goods industry relies on rubber-based adhesives for assembling and repairing shoes, bags, belts, and other leather products. These adhesives offer excellent bonding strength, flexibility, and resistance to wear and tear. They ensure that the bonded materials remain securely attached, even under constant use and stress.
5. Household and DIY Projects
For household and DIY enthusiasts, rubber-based adhesives are a go-to solution for a wide range of tasks. From repairing broken items to crafting projects, these adhesives provide reliable bonding for various materials. Their ease of use and versatility make them a staple in every toolbox.
Benefits of Rubber-Based Adhesives
Rubber-based adhesives offer numerous advantages that make them a popular choice for many applications. Here are some key benefits:
1. Versatility
One of the most significant advantages of rubber-based adhesives is their versatility. They can bond a wide range of materials, including metals, plastics, wood, glass, and fabrics. This makes them suitable for diverse applications across multiple industries.
2. Flexibility and Durability
The inherent flexibility of rubber-based adhesives allows them to accommodate the natural movements of bonded materials without losing their adhesion strength. This is particularly important in applications where materials expand, contract, or experience vibrations. The durability of these adhesives ensures long-lasting bonds that can withstand various environmental conditions.
3. Quick Bonding
Rubber-based adhesives, especially pressure-sensitive variants, offer quick bonding capabilities. They adhere instantly to surfaces with light pressure, eliminating the need for clamping or curing times. This quick bonding feature enhances productivity and efficiency in manufacturing and assembly processes.
4. Resistance to Environmental Factors
Rubber-based adhesives exhibit excellent resistance to environmental factors such as moisture, temperature fluctuations, and chemicals. This makes them suitable for outdoor and industrial applications where exposure to harsh conditions is common. The adhesives maintain their performance and integrity, ensuring reliable bonds over time.
5. Ease of Application
Rubber-based adhesives are easy to apply, whether in liquid, paste, or tape form. They can be dispensed using various methods, including brushes, rollers, sprayers, and automated equipment. This versatility in application methods ensures that users can choose the most convenient and efficient way to apply the adhesive for their specific needs.
Comparing Rubber-Based Adhesives to Other Adhesive Types
While rubber-based adhesives offer numerous benefits, it’s essential to understand how they compare to other adhesive types to make informed choices for specific applications. Let’s look at how rubber-based adhesives stack up against some common alternatives:
Rubber-Based Adhesives vs. Epoxy Adhesives
Rubber-Based Adhesives:
- Flexibility: High flexibility, ideal for applications requiring movement and vibration resistance.
- Curing Time: Quick bonding, especially pressure-sensitive variants.
- Temperature Resistance: Moderate resistance to high temperatures.
Epoxy Adhesives:
- Flexibility: Rigid bonds, not suitable for applications requiring flexibility.
- Curing Time: Longer curing times, often requiring precise mixing and application.
- Temperature Resistance: Excellent resistance to high temperatures and harsh environments.
Rubber-Based Adhesives vs. Cyanoacrylate Adhesives (Super Glue)
Rubber-Based Adhesives:
- Bonding Speed: Instant bonding for pressure-sensitive types, quick for contact adhesives.
- Material Compatibility: Bonds a wide range of materials.
- Flexibility: Provides flexible bonds.
Cyanoacrylate Adhesives:
- Bonding Speed: Very fast bonding, often within seconds.
- Material Compatibility: Bonds well to most materials but may have limited flexibility.
- Flexibility: Rigid bonds, not suitable for applications requiring movement.
Rubber-Based Adhesives vs. Hot Melt Adhesives
Rubber-Based Adhesives:
- Application Temperature: Applied at room temperature.
- Bond Strength: Strong, durable bonds with flexibility.
- Versatility: Suitable for various materials and applications.
Hot Melt Adhesives:
- Application Temperature: Requires heating to apply.
- Bond Strength: Strong bonds, but may become brittle in cold conditions.
- Versatility: Effective for specific applications but may not bond as well to some materials.
Choosing the Right Rubber-Based Adhesive
Selecting the right rubber-based adhesive for a specific application involves considering several factors:
1. Type of Material
Consider the materials to be bonded. Rubber-based adhesives are versatile, but certain formulations may be better suited for specific materials. For example, a PSA might be ideal for bonding plastics and metals, while a contact adhesive could be better for laminates and veneers.
2. Application Method
Choose an adhesive that aligns with your application method. For large surface areas, contact adhesives applied with brushes or rollers may be more efficient. For smaller, precise applications, PSAs in tape or liquid form might be more suitable.
3. Environmental Conditions
Consider the environmental conditions the adhesive will be exposed to. If the bonded materials will experience extreme temperatures, moisture, or chemicals, ensure the adhesive formulation offers the necessary resistance.
4. Bonding Requirements
Evaluate the bonding requirements, such as the need for flexibility, quick bonding, and durability. Choose an adhesive that meets these requirements to ensure a successful and long-lasting bond.
Conclusion
Rubber-based adhesives are a versatile and reliable solution for various bonding needs. At Super Bond Adhesives, we are committed to providing high-quality rubber-based adhesive products that meet the diverse demands of our customers. Whether you are in the automotive industry, construction, packaging, footwear, or simply tackling a DIY project, our rubber-based adhesives offer the strength, flexibility, and durability you need.
Understanding the unique properties and benefits of rubber-based adhesives allows you to make informed decisions and achieve optimal bonding results. With Super Bond Adhesives, you can trust that your bonding needs are in capable hands. Explore
To Know More Visit This Link – https://superbond.co.in/rubber-based-adhesives/