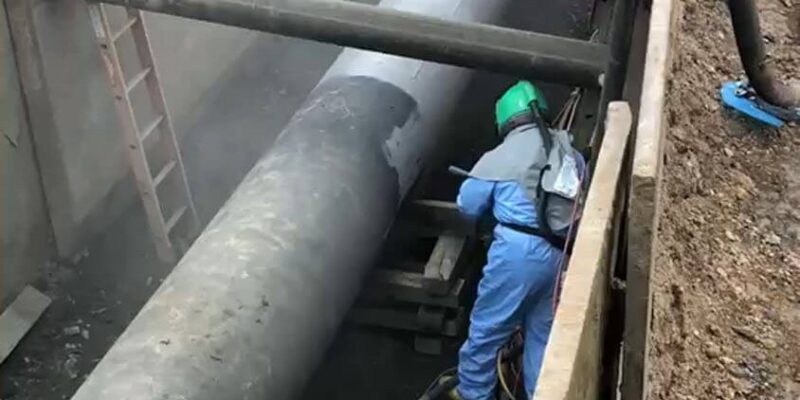
Introduction to Sandblasting
Sandblasting, also known as abrasive blasting, stands as a cornerstone in the realm of surface treatment and restoration. It’s a technique that has found its application across diverse industries, owing to its efficiency and versatility. In this comprehensive guide, we embark on an exploration of sandblasting, delving into its techniques, applications, benefits, safety measures, and the pivotal role played by NJ Reliable Coating in optimizing its outcomes.
Understanding Sandblasting
At its core, sandblasting involves the use of compressed air to propel abrasive materials onto a surface at high speeds. These abrasive materials, ranging from sand and silica to garnet or glass beads, effectively remove unwanted coatings, corrosion, rust, or imperfections from surfaces, leaving behind a clean and smooth finish. What distinguishes sandblasting is its ability to achieve this outcome with precision, ensuring the integrity of the underlying substrate remains intact.
Techniques of Sandblasting
- Pressure Blasting: In pressure blasting, abrasive materials are propelled using high-pressure air or water, resulting in a more aggressive and rapid cleaning or stripping process. This technique is particularly favored when dealing with stubborn contaminants or thick coatings.
- Siphon Blasting: Utilizing a siphon system, this technique creates a vacuum that draws abrasive material into the air stream. It offers versatility and cost-effectiveness, making it suitable for a wide array of applications.
- Wet Blasting: Wet blasting involves the addition of water to the abrasive material stream. This not only reduces dust emissions but also minimizes heat buildup, enabling a gentler cleaning action suitable for delicate surfaces.
Applications of Sandblasting
- Surface Preparation: Sandblasting serves as a crucial step in preparing surfaces before painting, coating, or bonding. By removing contaminants and creating a clean substrate, it ensures better adhesion and longevity of the applied finish.
- Rust and Corrosion Removal: One of the primary applications of sandblasting is the removal of rust, corrosion, and old paint from metal surfaces. This restoration process rejuvenates the material, restoring it to its original condition.
- Graffiti Removal: Sandblasting is an effective method for removing graffiti from various surfaces, including concrete, brick, and metal. By eradicating unwanted markings, it restores the aesthetics of the affected area.
- Monument Restoration: In the realms of art and conservation, sandblasting finds its niche in the restoration of monuments, sculptures, and historical buildings. By delicately removing layers of grime and corrosion, it preserves the beauty and integrity of these cultural artifacts.
- Deburring and Surface Finishing: Sandblasting is employed for deburring and finishing metal components, enhancing their surface quality and functionality. Whether it’s smoothing rough edges or achieving a precise surface texture, sandblasting delivers consistent results.
Benefits of Sandblasting
- Versatility: Sandblasting’s adaptability to a wide range of surfaces and materials makes it a versatile solution for diverse applications. Whether it’s metal, concrete, wood, or stone, sandblasting can be tailored to suit the specific requirements of the project.
- Efficiency: Sandblasting offers a fast and efficient cleaning and stripping process, reducing downtime and labor costs associated with traditional methods. Its ability to remove multiple layers of coatings in a single pass streamlines the restoration process.
- Precision: With sandblasting, operators have precise control over the removal process, ensuring uniformity and consistency in the finished surface. This level of precision is essential, especially in industries where quality and accuracy are paramount.
- Environmental Friendliness: When coupled with proper containment and recycling systems, sandblasting can be environmentally friendly. By minimizing waste and emissions, it aligns with sustainable practices, making it a preferred choice for environmentally conscious projects.
Safety Measures
- Personal Protective Equipment (PPE): Operators should wear appropriate PPE, including respirators, goggles, gloves, and protective clothing, to prevent exposure to abrasive materials and dust. This safeguards against respiratory issues and minimizes the risk of injury.
- Ventilation: Adequate ventilation systems should be in place to remove dust and abrasive particles from the work area, maintaining air quality and mitigating health risks. Proper ventilation also contributes to operator comfort and productivity.
- Training: Proper training and certification are imperative for operators to understand the equipment, techniques, and safety protocols associated with sandblasting. Ongoing training ensures competency and promotes a culture of safety within the workplace.
- Equipment Maintenance: Regular inspection and maintenance of sandblasting equipment are crucial for ensuring safe and efficient operation. By addressing potential issues proactively, operators can minimize the risk of accidents and equipment breakdowns.
NJ Reliable Coating: Enhancing Sandblasting Results
NJ Reliable Coating stands as a beacon of excellence in the realm of coating solutions. Specializing in providing high-quality coatings for various industries, NJ Reliable Coating complements the sandblasting process by offering durable and protective coatings that enhance the longevity and performance of treated surfaces. Their expertise and commitment to quality ensure that each project receives tailored solutions designed to meet its specific requirements.
Conclusion
Sandblasting, coupled with the expertise of NJ Reliable Coating, offers a formidable combination for achieving optimal surface treatment and restoration results. From surface preparation to corrosion removal and beyond, sandblasting remains a cornerstone of numerous industries, thanks to its efficiency, precision, and versatility. By prioritizing safety, environmental responsibility, and the utilization of expert coating solutions, professionals can harness the full potential of sandblasting to preserve, protect, and enhance the surfaces that shape our world.