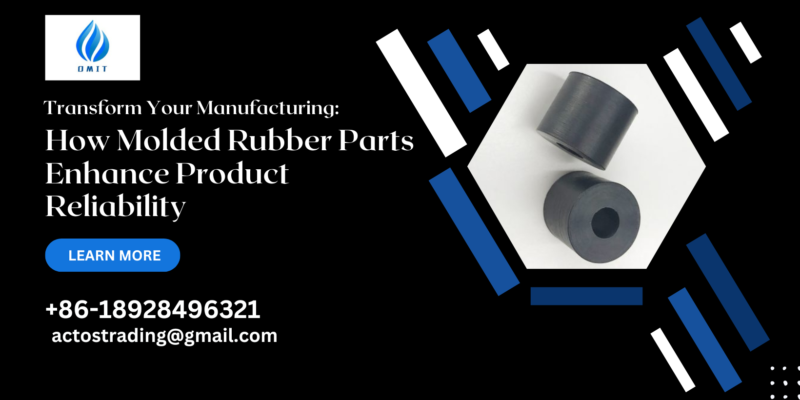
In today’s competitive manufacturing landscape, innovation is key to standing out. One technology that has been making waves in product manufacturing is the use of molded rubber parts. These versatile components offer a myriad of advantages, particularly when it comes to enhancing product reliability. With businesses looking for ways to improve the durability, longevity, and overall performance of their products, molded rubber parts have emerged as a game-changer.
What Are Molded Rubber Parts?
Molded rubber parts are precisely shaped components that are formed by injecting rubber materials into molds. This process allows for a high level of customization and is widely used across various industries to create components that are durable, flexible, and reliable. From seals to gaskets, bumpers to bushings, molded rubber parts serve countless functions in manufacturing.
Why Molded Rubber Parts Are Critical for Modern Manufacturing
The appeal of molded rubber parts lies in their ability to enhance several key aspects of product manufacturing. By using molded rubber components, manufacturers can improve product durability, lower maintenance costs, and ensure that their products can withstand harsh environmental conditions.
Enhancing Durability
One of the most compelling reasons to use molded rubber parts is their durability. These parts are designed to resist wear and tear, ensuring that the products they are integrated into last longer, even in demanding conditions. Whether exposed to extreme temperatures, chemicals, or physical stress, molded rubber parts provide a resilient solution.
Reducing Maintenance Costs
With greater durability comes reduced maintenance needs. Products utilizing molded rubber parts often require less frequent repairs and replacements, lowering the overall cost of ownership for the end user. This is particularly valuable in industries such as automotive and aerospace, where equipment downtime can be both costly and dangerous.
Versatility in Applications
From automotive to aerospace, electronics to medical devices, the versatility of molded rubber parts is evident. Their adaptability allows manufacturers to use them in a wide range of applications, each requiring specific properties such as resistance to chemicals, heat, and pressure.
Key Benefits of Using Molded Rubber Parts
Improved Product Reliability with Molded Rubber Parts
When integrated into manufacturing processes, molded rubber parts contribute significantly to improving the reliability of the final product. For instance, rubber gaskets ensure tight seals, preventing leaks in industrial machinery. Similarly, rubber bumpers help absorb shocks and protect sensitive components in consumer electronics.
By ensuring consistent performance across a wide range of environments, molded rubber parts help manufacturers create products that customers can trust.
Environmental Resistance: Weather, Chemicals, and Heat
Molded rubber parts are known for their ability to withstand harsh environmental conditions. Whether it’s extreme heat in an automotive engine or exposure to chemicals in industrial settings, rubber components perform consistently. This makes them a preferred choice for outdoor applications or industries where environmental factors are a concern.
How Molded Rubber Parts Reduce Maintenance Costs
Reducing downtime is essential for any manufacturer. Molded rubber parts, thanks to their durability, contribute to longer intervals between maintenance checks. For example, rubber seals used in machinery prevent fluid leaks, reducing the need for frequent repairs. Businesses benefit from this efficiency through reduced operational expenses and increased profitability.
Versatility in Applications Across Industries
- Automotive Industry: Enhancing Safety and Performance
In the automotive industry, molded rubber parts play a critical role in improving vehicle performance and safety. Rubber components such as vibration dampers and seals are used to minimize noise, reduce vibrations, and ensure the smooth operation of engines and other parts. - Aerospace Industry: Lightweight but Durable Components
The aerospace sector benefits from the lightweight yet durable nature of molded rubber parts. These components help improve fuel efficiency by reducing the weight of aircraft, all while maintaining high performance under extreme conditions. - Medical Devices: Reliability in Life-Saving Equipment
In medical devices, reliability is paramount. Molded rubber parts are used in life-saving equipment, where they must meet strict hygiene and durability standards. Rubber components like seals and diaphragms ensure that devices perform reliably in critical medical environments.
The Customization Advantage of Molded Rubber Parts
One of the key benefits of molded rubber parts is their ability to be customized to meet specific manufacturing needs. Whether it’s creating a unique shape for a particular application or selecting a rubber material with specialized properties, custom molding allows manufacturers to tailor parts for optimal performance.
How Molded Rubber Parts Improve Sustainability in Manufacturing
Sustainability is becoming increasingly important in manufacturing, and molded rubber parts offer an eco-friendly solution. Many rubber components can be produced using recycled or sustainable materials, reducing the environmental impact of manufacturing. Additionally, the durability of these parts means fewer replacements, further minimizing waste.
Future Trends in Molded Rubber Technology
As technology continues to advance, so too will the capabilities of molded rubber parts. Innovations in material science are expected to lead to even more durable and versatile rubber components, while advancements in automation will make the molding process faster and more efficient.
Molded rubber parts are revolutionizing the manufacturing process by enhancing product reliability, reducing costs, and offering a versatile solution for various industries. Whether you are in the automotive, aerospace, or medical sector, incorporating molded rubber parts into your products can lead to significant improvements in performance and durability. As we look to the future, the continued evolution of rubber molding technology promises even greater benefits for manufacturers.
FAQs
1. What are molded rubber parts made of?
Molded rubber parts are typically made from natural or synthetic rubber compounds, which can be customized for specific applications.
2. How do molded rubber parts improve product reliability?
They offer enhanced durability, environmental resistance, and customizability, ensuring products perform consistently under challenging conditions.
3. Can molded rubber parts be customized for any application?
Yes, molded rubber parts can be tailored to meet the specific requirements of various industries, from automotive to medical devices.
4. Are molded rubber parts eco-friendly?
Yes, many molded rubber parts can be made from sustainable or recycled materials, contributing to a more eco-friendly manufacturing process.
5. How do molded rubber parts reduce maintenance costs?
Their durability and resistance to wear reduce the need for frequent repairs and replacements, leading to lower maintenance costs over time.